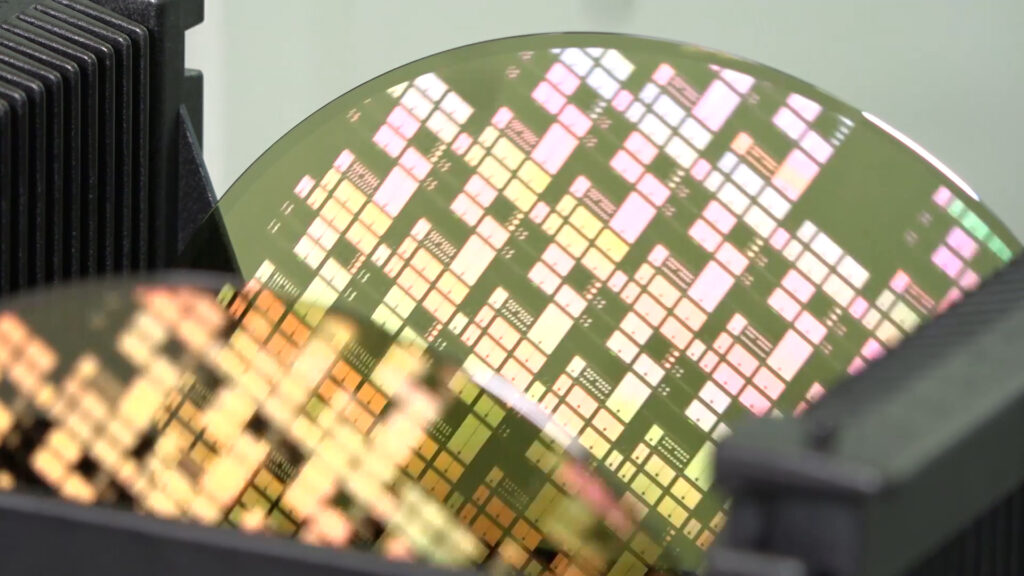
The coming years will see the market for electronic devices and logic boards grow by additional leaps and bounds. But as electronics and semiconductors infiltrate new industries and products, designers and manufacturers are always on the hunt for better and smarter ways to manufacture these vital components.
Silicon carbide semiconductors are one such development. But to what do we owe their growth in popularity? And which devices have made the switch — or plan to in the near future? To get such questions answered, one should first be familiar with the terms like semiconductor. So, first thing first, we’re first going to state what a semiconductor is along with the different purposes a semiconductor serves and finally proceeding towards Silicon Carbide as a semiconductor.
What is a Semiconductor?
Semiconductors are special materials whose electrical conductivity lie somewhere between what you would see with a conductor (such as copper wire) and what you would see with an insulator (a ceramic-like glass). A semiconductor’s conductivity can be varied by adding certain additional elements, called impurities.
Silicon (Si) is an example of a pure semiconductor commonly used in electronics. Germanium (Ge) is another pure semiconductor that was used with some of the earliest electronic devices. Semiconductors are also made from compounds, including Gallium arsenide (GaAs), Gallium nitride (GaN), Silicon Germanium, (SiGe), and Silicon carbide (SiC).
Commercial applications of Silicon Carbide
Nearly every electronic item you encounter on a day-to-day basis contains semiconductors. They are found in everything from your smartphone or tablet, to even higher power applications such as server farms and solar arrays.
More specifically, semiconductors are a key part of the components that make up electronic systems, including ICs (integrated circuits) diodes, transistors, and MOSFETs (Metal Oxide Semiconductor Field Effect Transistors), to name a few. These systems are among the many building blocks that make up electronic systems, and the existence of semiconductors makes all of this possible.
What is a Silicon Carbide Semiconductor?
Silicon carbide (SiC), also known as carborundum, is a semiconductor containing silicon and carbon. It occurs in nature as the extremely rare mineral moissanite. Synthetic SiC powder has been mass-produced since 1893 for use as an abrasive. Grains of silicon carbide can be bonded together by sinteringto form very hard ceramics that are widely used in applications requiring high endurance, such as car brakes, car clutches and ceramic plates in bulletproof vests. Electronic applications of silicon carbide such as light-emitting diodes (LEDs) and detectors in early radios were first demonstrated around 1907. SiC is used in semiconductor electronics devices that operate at high temperatures or high voltages, or both.
The 2 most salient features have made Silicon Carbide a big game changer
1. Silicon Carbide Withstands Higher Voltages
Power semiconductors made from silicon carbide are capable of withstanding voltages up to 10 times higher than ordinary silicon. This, in turn, has a number of implications for system complexity and cost.
Because SiC tolerates higher voltages, power systems built on silicon carbide semiconductors require fewer switches in series. This means simpler and more reliable system layouts as well as lower costs for manufacturers thanks to a reduced number of components.
2. Silicon Carbide Operates at Higher Temperatures
The proliferation of electronic products throughout the world means many types of devices that must operate in variable or harsh conditions, such as higher temperatures. Silicon carbide shines here as well.
Common silicon IGBTs demonstrates a relatively poor degree of thermal conductivity. Power semiconductors made from silicon are generally rated to operate as expected in temperatures no greater than 150°C. In comparison, SiC semiconductors can maintain functionality and integrity at temperatures of 200°C or more, thanks to a thermal conductivity that improves upon common silicon by a factor of three. However, most commercial-level semiconductors of this type still receive a recommended temperature rating of 175°C or thereabouts.
As with the higher voltage ratings mentioned previously, higher temperature ratings also play their part in reducing system design complexity, increasing reliability and lowering costs for manufacturers. Thanks to SiC semiconductors, system designers can use smaller and fewer capacitors and storage inductors, which brings down the total cost of the electrical system.
Silicon v/s Silicon carbide: It’s always silicon carbide over silicon
Silicon is probably the most popular semiconductor in the world today, but that does not mean it’s always the best choice for electronics. One of its main competitors, silicon carbide, is at the forefront when it comes to power electronics.
Power electronics are used in just about any type of design that depends on power, whether it is converting DC solar power to AC power for your home or helping to regulate the battery power in your hybrid electric vehicle. Power electronics even come into play with the power converters you use in so many of the devices around your home.
A major element of power electronics is the bandgap, or energy gap, of the semiconductor it contains. When a semiconductor has a higher bandgap, the electronics that use it can be smaller and operate much faster and more reliably. It can also function at higher temperatures, higher voltages, and higher frequencies than other semiconductors — and that is the case with silicon carbide. While silicon has a bandgap around 1.12, silicon carbide sits at 3.26.
Power electronics — especially MOSFETs — must be able to handle extremely high voltages, referred to as the critical breakdown strength. Silicon carbide offers significantly higher breakdown strength than silicon, meaning it can handle higher voltages in a smaller size and support higher MOSFET blocking voltages.
Thermal conductivity (which relates to how fast a semiconductor can get rid of the heat that it generates) is another important property. If a semiconductor is not effective at dissipating heat, that severely limits the operational voltages and temperature ranges semiconductor components can handle. This is another area where silicon carbide outperforms silicon: the thermal conductivity of silicon carbide is 1490 W/m-K compared to 150 W/m-K for silicon.
Silicon Carbide MOSFETs: Proven Reliability and Performance
Semiconductors have the unique property of possessing electrical conductivity somewhere between a conductor and an insulator. It is this property that makes devices such as transistors, diodes, and MOSFETs possible — and from those devices come the electronic systems we all rely on every day of our lives. While there are several different semiconductors in use today, silicon carbide offers unique solutions and key performance advantages over other commonly used materials.
SiC Devices have reshaped the Semiconductor Sector
The third generation of silicon carbide (SiC)semiconductor has delivered remarkable performance with practical benefits in a growing number of applications. But with the pace of innovation rapidly increasing in sectors such as electric vehicles (EVs), renewable energy, and 5G, engineers are increasingly looking for new solutions and demanding more from power switch technology to meet consumer and industry demand.
Silicon carbide’s constituents, carbon and silicon, are respectively the fourth and eighth most abundant elements in the galaxy. Despite this, it rarely appears naturally on earth with just minute traces found in meteorites and some rock deposits. It can be produced synthetically quite easily though, and has been used as an abrasive (carborundum), for more than a century.
In power electronics, we now know SiC as a wide bandgap (WBG) semiconductor which has revolutionized power conversion performance, yielding efficiency figures previously unattainable at high frequencies, with further knock-on benefits of smaller associated passive components, particularly magnetics. That all comes with cost, weight, and size savings.
Industrial utilization of the well-known Silicon Carbide semiconductor
Increasingly, the automotive market is “ground zero” for demand and innovation in silicon carbide semiconductors. Between 2016 and 2017, the market for SiC power devices jumped from $248 million to $302 million. Companies like Tesla, Toyota and others, who lead the pack in terms of electric vehicle innovation, are big reasons for this higher demand.
Electric and driverless vehicles with onboard charging units and traction inverters are prime candidates for SiC semiconductors. But these are far from the only high-voltage applications to which SiC MOSFETs are well suited. Here are some of the other industries and products where silicon carbide is finding a home in power system design:
- Military systems
- Sensor systems
- Solar power inverters and other power supplies
- Wind turbines
SiC is part of a hierarchy of semiconductor materials that meets a range of power needs. Common silicon has historically been the material of choice for power requirements of five volts or below. Then came Gallium-Nitride (GaN), which performs well in systems ranging up to 1,000 volts. SiC has emerged as the semiconductor material of choice for system designs that must accommodate 1,000 volts or more.SiC and GaN were developed and came into vogue more-or-less in tandem, but SiC has “caught on” in the market in a way GaN has not.
According to experts, using SiC in electric motors can reduce power loss by an impressive 80 percent. In turn, this means designers can incorporate smaller batteries, but enjoy lower power requirements and costs, without sacrificing product performance.