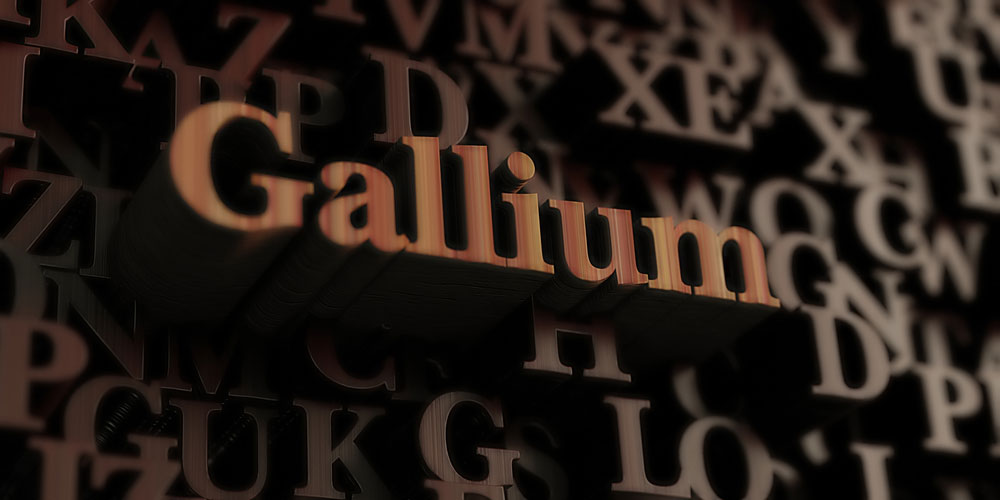
Integrated circuits made on thin layers hold promise for developments including improved thermal characteristics, lightweight stackability and a high degree of flexibility compared to conventionally thick substrates.
Now in a significant advance, researchers from IBM have successfully used a simple technique to remove thin layers from otherwise thick, rigid GaN semiconductor crystals without causing crystalline damage. They describe the ‘controlled spalling’ layer transfer technique in the latest issue of the Journal of Applied Physics, from AIP Publishing.
The technique also makes it possible to measure basic physical properties of the material system, like strain-induced optical effects and fracture toughness, which are otherwise difficult to measure. Single-crystal GaN wafers are extremely expensive, where just one 2-inch wafer can cost thousands of dollars, so having more layers means getting more value out of each wafer. Thinner layers also provide performance advantages for power electronics, since it offers lower electrical resistance and heat is easier to remove.
“Our approach to thin film removal is intriguing because it’s based on fracture,” said Stephen W. Bedell, research staff member at IBM Research and one of the paper’s authors. “First, we first deposit a nickel layer onto the surface of the material we want to remove. This nickel layer is under tensile strength – think drumhead. Then we simply roll a layer of tape onto the nickel, hold the substrate down so it can’t move, and then peel the tape off. When we do this, the stressed nickel layer creates a crack in the underlying material that goes down into the substrate and then travels parallel to the surface.”
Their method boils down to simply peeling off the tape, nickel layer and a thin layer of the substrate material stuck to the nickel. “A good analogy of how remarkable this process is can be made with a pane of glass,” Bedell said. “We’re breaking the glass in the long direction, so instead of a bunch of broken glass shards, we’re left with two full sheets of glass. We can control how much of the surface is removed by adjusting the thickness of the nickel layer. Because the entire process is done at room temperature, we can even do this on finished circuits and devices, rendering them flexible.”
The method appears to be the simplest way of transferring thin layers from thick substrates. And it may well be the only layer transfer method that’s materially agnostic. “We’ve already demonstrated the transfer of silicon, germanium, GaAs, GaN/sapphire, and even amorphous materials like glass, and it can be applied at nearly any time in the fabrication flow, from starting materials to partially or fully finished circuits,” Bedell said.
“The basic mechanism of substrate spalling fracture started out as a materials science problem,” he said. “It was known that metallic film deposition would often lead to cracking of the underlying substrate, which is considered a bad thing. But we found that this was a metastable phenomenon, meaning that we could deposit a thick enough layer to crack the substrate, but thin enough so that it didn’t crack on its own – it just needed a crack to get started.”
Their next discovery was how to make the crack initiation consistent and reliable. While there are many ways to generate a crack – laser, chemical etching, thermal, mechanical, etc. It turns out that the simplest way is to terminate the thickness of the nickel layer very abruptly near the edge of the substrate. “This creates a large stress discontinuity at the edge of the nickel film so that once the tape is applied, a small pull on the tape consistently initiates the crack in that region,” he said.
Controlled spalling has already been used to create extremely lightweight, high-efficiency GaAs-based solar cells for aerospace applications and flexible state-of-the-art circuits.
The group is now working with research partners to fabricate high-voltage GaN devices using this approach. “We’ve also had great interaction with many of the GaN technology leaders through the Department of Energy’s ARPA-E SWITCHES program and hope to use controlled spalling to enable novel devices through future partnerships,” Bedell said.