- A level sensor is a device for determining the level or amount of fluids, liquids, or other substances that flow in an open or closed system. There are two types of level measurements, namely, continuous and point level measurements.
- Continuous level sensors are used for measuring levels to a specific limit, but they provide accurate results. Point level sensors, on the other hand, only determine if the liquid level is high or low.
- The level sensors are usually connected to an output unit for transmitting the results to a monitoring system. Current technologies employ wireless transmission of data to the monitoring system, which is useful in elevated and dangerous locations that cannot be easily accessed by common workers.
Types of Level Sensors
Ultrasonic Level Sensors
- Ultrasonic level sensors are used for detecting the levels of viscous liquid substances and bulk materials as well. They are operated by emitting acoustic waves at a frequency range of 20 to 200 kHz. The sound waves have then reflected a transducer.
- The response of ultrasonic sensors is influenced by pressure, turbulence, moisture, and temperature. In addition, the transducer is required to be mounted appropriately to obtain a better response.
- Pros – No moving parts, compact, reliable, not affected by media properties.
- Applications – Noncontact applications with highly viscous and bulk solids. Used in systems that require remote monitoring.
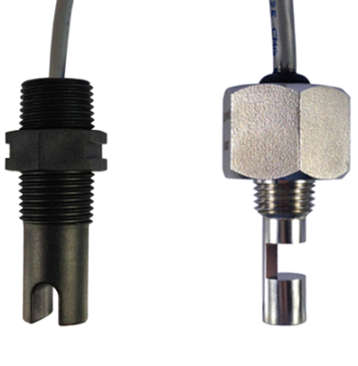
Capacitance Level Sensors
- Capacitance level sensors are used for detecting the levels of aqueous liquids and slurries. They are operated by employing a probe for monitoring level changes. These changes are converted into analog signals.
- Capacitance sensors are easy to use and clean as they do not have any moving components. They are commonly employed in applications involving high temperature and pressure.
- Pros – Solid-state, can be non-invasive, compact, accurate.
- Cons – May require calibration, can only be used in certain liquids.
- Applications – Tank level monitoring in chemical, food, water treatment, power, and brewery industries.
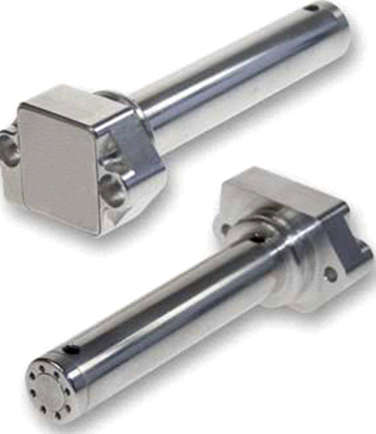
Optical Level Sensors
- Optical level sensors detect liquids containing suspended materials, interface between two immiscible liquids, and the presence of sediments. They are operated based on the transmission changes of infrared light emitted from an infrared LED. The interference from the emitted light can be eliminated by employing a high-energy infrared diode and pulse modulation methods.
- Continuous optical level sensors, on the other hand, employ highly concentrated laser light that can permeate dusty environments and detect liquid substances. However, its application is limited to industries due to maintenance and high cost.
- Pros – Compact, no moving parts, high pressure, and temperature capability, can detect tiny amounts of liquids.
- Cons – Invasive as the sensor requires contact with the liquid, requires power, and certain thick substances can cause the coating on the prism.
- Applications – tank level measurement and leak detection applications.
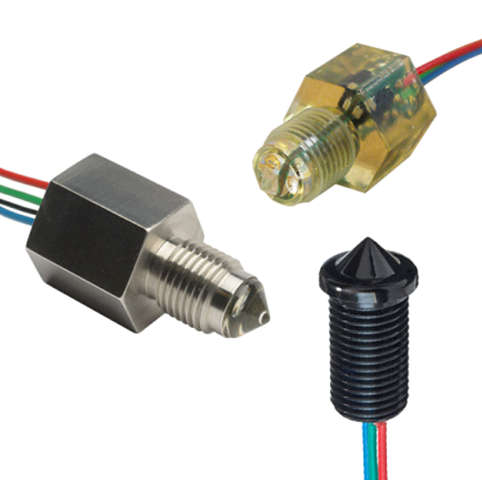
Microwave Optical Sensors
- Microwave level sensors are used for applications involving varying temperature and pressure, and dusty and moist environments, as microwaves can easily penetrate under these conditions without requiring air molecules for energy transmission. These sensors can detect conductive water and metallic substances. The measurements are carried out using time domain or pulse reflectometry.
- However, complex arrangement and high cost are the major disadvantages of microwave sensors.
- Pros – very accurate, no calibration required, multiple output options.
- Cons – expensive, can be affected by the environment, limited detection range.
- Applications – Moist, vaporous, and dusty environments. They are also used in systems in which temperatures vary.
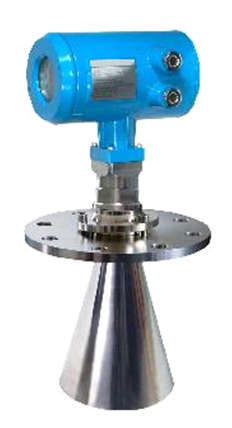
Float Switch
- Float switches are one of the most cost-effective but also well-proven technologies for water level sensing. A float switch includes a magnet within a float and a magnetic reed switch contained within a secure housing. The float moves with the change in liquid and will cause the reed switch to either open or close depending on if it’s in air or liquid. Although simple in design, this technology offers long-term reliability at an attractive price point.
- Pros- Non-powered, direct indication, relatively inexpensive, various outputs.
- Cons- Invasive, moving parts, large in size, a large amount of liquid has to be present before the float makes contact.
- Applications- Tank level applications where water, oil, hydraulic fluids, and chemicals are being used.
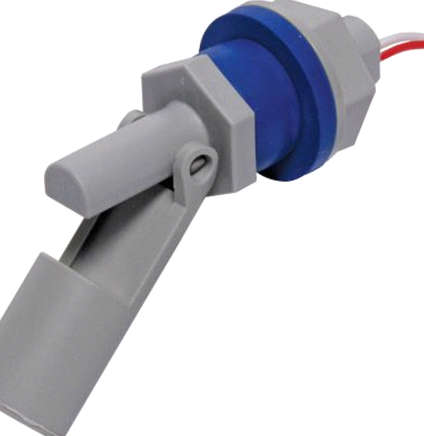
Conductive or Resistance level sensor
- Conductive sensors are used for point-level sensing conductive liquids such as water and highly corrosive liquids. Simply put, two metallic probes of different lengths (one long, one short) insert into a tank. The long probe transmits a low voltage, the second shorter probe is cut so the tip is at the switching point. When the probes are in liquid, the current flows across both probes to activate the switch. One of the benefits of these devices is that they are safe due to their low voltages and currents. They are also easy to use and install but regular maintenance checks must be carried out to ensure there is no build-up on the probe otherwise it will not perform properly.
- Pros – No moving parts, easy to use, low-cost.
- Cons – Invasive, liquids need to be conductive, probe erosion.
- Applications – Tank level measurement for boiler water, reagent monitoring, highly corrosive liquids.
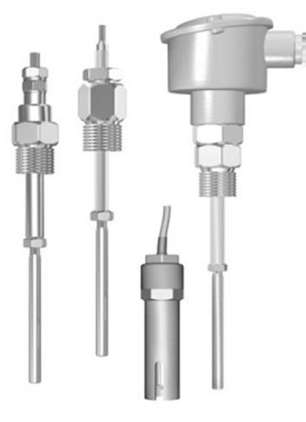
Vibrating or Tuning Fork
- The vibrating sensor technology is perfect for solid and liquid level control, including sticky materials and foam, as well as powders and fine-grained solids. However, the types of applications that can use tuning forks are limited to overfill or run dry type applications and they do not provide continuous process measurement. However can be used in conjunction with continuous level detection systems, acting as alarm points for over-filling and leaks.
- Pros – Compact, cost-effective.
- Cons – Invasive, number of uses are limited.
- Applications – level control of liquid, powders, and fine-grained solids within mining, chemical processing, and food and beverage industries.
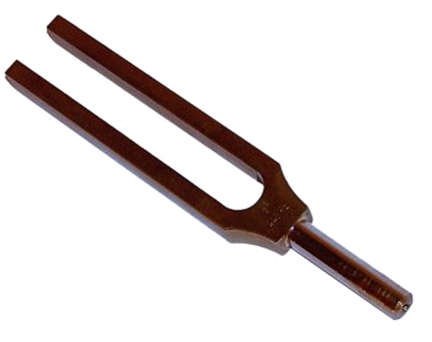