- A brushless DC electric motor (BLDC motor or BL motor), also known as an electronically commutated motor (ECM or EC motor) or synchronous DC motor, is a synchronous motor that uses a direct current (DC) electric power supply.
- It is a type of synchronous motor in the sense that the magnetic field generated by the stator and the rotor revolve at the same frequency.
There are two types of commonly used DC Motors
-
- Brushed Motors
- Brushless Motors (or BLDC Motors)
- As their names imply, DC brushed motors have brushes, which are used to commutate the motor to cause it to spin. Brushless motors replace the mechanical commutation function with electronic control.
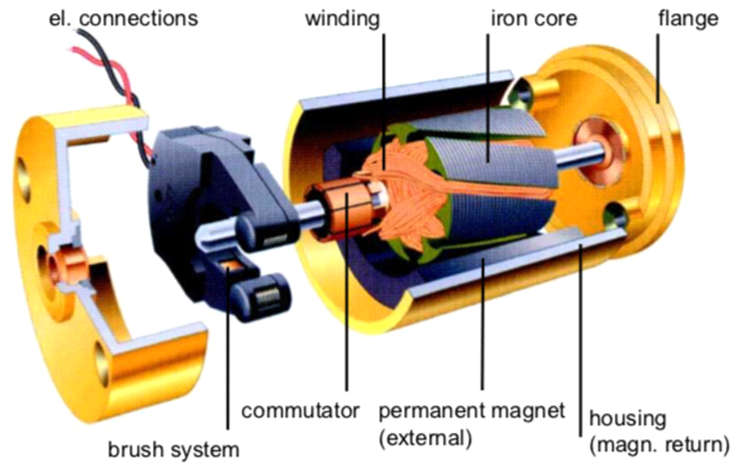
- It is a high-performance motor that provides large torque per cubic inch over a vast speed range. BLDC motors do not have brushes which make them more reliable, have high life expectancies, and maintenance-free operation. There are no ionizing sparks from the commutator, and electromagnetic interference is also get reduced.
Working Principle of Brushless DC Motors
- BLDC motor uses permanent magnets, instead of electromagnets that are used in conventional motors. The permanent magnets of BLDC motors have less energy and heat losses compared to electromagnets.
- They use an inverter to convert from DC to a waveform which switches to activate the windings of the motor as required.
- BLDC motors have 85 to 90 percent efficiency margins, which is higher than the standard brushed motors at 75 to 80 percent. Brushless DC motors must also be electronically commutated, which means the motor is regulated by a control mechanism.
- BLDC motors are successfully used in automotive, HVAC, electronic, computer, semiconductor, and medical industries. Also, they are used in industrial applications such as actuators, feed drives for CNC machines, industrial robots, and extruder drives, among others.
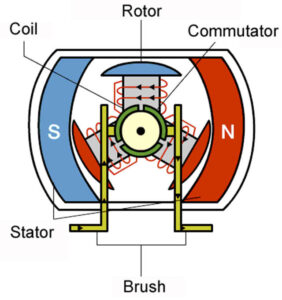
- The cost of a brushless DC motor is comparatively higher compared to a brushed DC motor. When the Brushless DC motor is operated at low-speed slight vibrations occur during low-speed rotation.
- BLDC motors are available in three configurations: single-phase, two-phase, and three-phase. Out of these, the three-phase BLDC is the most common
- They are also compact and provide high torque with better speed control and efficiency.
Also, it has a few disadvantages like higher cost, resonance issues, and complex wiring setup due to the involvement of electronic control. - When supplied Current through a winding, it generates a magnetic field, which in the presence of a second magnetic field (typically initiated by permanent magnets) generates a force on that winding that reaches a maximum when its conductors are at 90° to the second field.
- BLDC motors are with quiet running characteristics, high acceleration rates, long service life, and speeds of up to 14,000 rpm.
Advantages of Brushless DC Motors
- Better speed versus torque characteristics.
- High dynamic response.
- High efficiency.
- Long operating life due to a lack of electrical and friction losses.
- Noiseless operation.
- Higher speed ranges.