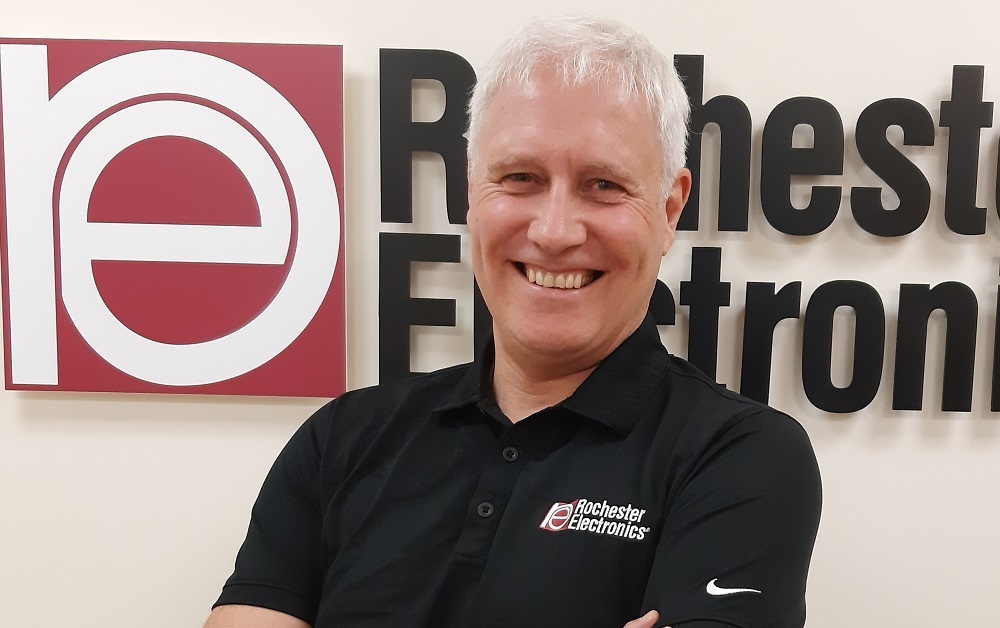
By Ken Greenwood, Technical Sales Manager EMEA , Rochester Electronics
The myths and the methods used to uncover the truth.
Counterfeits come in many guises. The most basic definition of a Counterfeit is “an imitation intended to be passed off fraudulently or deceptively as genuine, for profit.”
In times of supply shortage, or where component obsolescence limits availability, the prevalence of counterfeit devices often multiplies.
As awareness increases, so does sophistication.
We have moved far beyond incorrect manufacturers logos and IC packages with no die inside caught by the simplistic visual inspection testing used by those following AS6081. The Counterfeiters now have very sophisticated operations as the potential gains can be enormous.
Customers whose normal supply routes prove insufficient may assume unauthorised or gray market sources are the only solution; and that “Testing” can eliminate quality risks. Nothing could be further from the truth; but there ARE zero-risk sourcing options available.
What is a Counterfeit Semiconductor?
In the Semiconductor world Counterfeits include:
- Non-Functional or scrap product which is re-marked as good and re-sold.
- Functional yet sub-standard product purchased by the counterfeiter remarked and re-sold as full grade product at an increased price.
- Re-cycled and recovered components re-sold as new.
In all these cases, the process of etching back the original external markings with aggressive chemicals or even mechanical grinders can result in internal bond or substrate damage. Or the chemical residues from the cleaning process, slowly enter and contaminate the device, causing bond-pad or bond-wire failures in-service.
The process of recovering previously used semiconductors from old PCB’s can also result in catastrophic heat and/or mechanical damage. Recovery of the IC from the PCB itself is normally the last step of a long scrap trail which includes; a previous working life; and a return-for-recovery route through an uncontrolled storage environment. Exposure to excessive humidity, water, and salt is often routine. This process can produce an authentic used product that has questionable reliability. Authenticity does not automatically mean Reliability.
Identifiable surplus stock and traceability provides no guarantee regarding the storage conditions encountered during the components complete shelf-life.
The consequences of allowing sub-standard product to enter the supply chain may include:
- Reduced production yields and increased rework.
- Increased in-service failures and reduced reliability.
- Heightened risks and financial liability associated with catastrophic system failure.
- Cost of reputational damage.
What does “100% Tested” REALLY mean?
Customers may incorrectly assume “Testing” provides a 100% genuine guarantee. At its most basic, 3rd party testing comprises one or some of the following:
- Paperwork and Visual Inspection: Unlikely to identify the professional counterfeit devices. Traceability documents & certificates are also regularly forged to support the overall deception.
- X-Ray Inspection: Unlikely to identify fraudulently up-screened, well-marked recovered & re-used, or recovered failed-test devices.
- Basic Continuity or Functional Testing: Will not identify the fraudulently upscreened or well-marked recovered & re-used devices
- Full Functional Testing: The datasheet only provides a subset of the characteristics tested by the Original-Chip-Manufacturer (OCM).
Is Functional Testing carried out over the full temperature range?
When functionally testing a device, FAULT COVERAGE is critical. Without 100% test fault coverage, the device WILL have residual failures. Residual failures are devices that contain faults, but which PASS the testing used.
Example of Basic Functional Testing: Simple Traffic Controller:
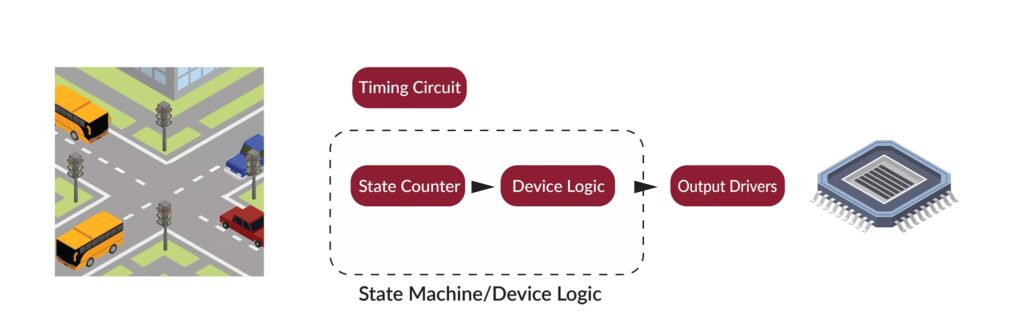

If the stuck-at condition above is not tested, then fault coverage is 98.96%. Is this acceptable in your critical application?
Semiconductor test is an intangible process – easy to conceptually understand – difficult to technically implement.
Effective test requires high fault coverage and accurate fault modeling. AS6171 calls out far greater testing for parts bought through Independent Distribution and yet is rarely followed.
The only way to offer a 100% guarantee that a device operates to its specification, is to test it using the original component manufacturer’s (OCM) test processes. However, even the most basic MCU test, as carried out by the OCM, comprises many 100,000’s of man-hours in development.
Third-Party Test Houses cannot hope to replicate these complex test processes, often only partial electrical and/or functional testing is carried out.
The following table referencing standards shows very clearly the only risk-free solution is fully authorized:

The ultimate tool in the fight against Counterfeit is AUTHORISATION.
AUTHORISED After-Market Suppliers and Manufacturers (as called out in the US-DoD DFARS), such as Rochester Electronics, provide the only 100% guaranteed and counterfeit-free source for active-shortage and obsolete semiconductors.
Finished devices stored and supplied by authorised sources are guaranteed to come only from the OCM and to have been stored in-line with the OCM’s recommendations. These products offer a 100% conformance guarantee.
As a licensed manufacturer, Rochester Electronics are also able to offer ongoing production of obsolete devices. Built from known-good-die, these products are tested using the OCM test procedures and, in many cases, the original test equipment – Guaranteed 100% compliant to the original specification.
Rochester Electronics is authorised by the OCM to mark their products with the original part number and the current date-code. Many of these devices are still in production 20 years after the original discontinuation.