- Film Capacitor is one of the most popular and widely used capacitors. These possess a difference in their properties of dielectric. In the modern type of film capacitor, there is the ‘direct electrical connection’ establishment with the electrodes that are present on both the windings. This keeps the path of the current to the electrode very short. This capacitor has various benefits it has very low ESR(ohmic resistance) and ESL(Parasitic Inductance). This can be preferred in various AC applications.
What is Film Capacitor?
- A capacitor that uses a slight plastic film like a dielectric is known as a film capacitor.
- A Film capacitor is reasonably inexpensive, constant overtime, and constant overtime n includes equivalent series inductance (ESR) and low self-inductance, while some film capacitors can withstand large reactive power values.
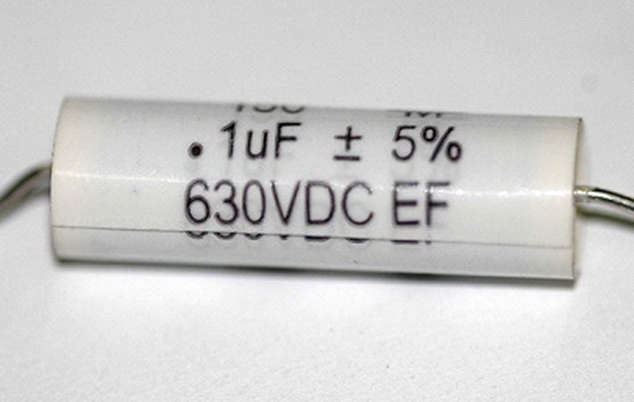
- The dielectric characteristics of the film capacitor are different. The dielectric used in this sort of capacitor can be any form of film. There is a ‘direct electrical connection’ establishment with the electrodes that are present on both windings in the modern form of film capacitor. This reduces the current’s route to the electrode to a minimum.
- Film capacitor is relatively simple to analyze and build. It is well-known for its dependability. This sort of capacitor is inexpensive to produce. The use of this capacitor reduces losses even on transmissions with high frequencies. Its structure is made of “Plastic Films.” These films are made to be very thin. Once the “Film drawing procedure” is done, the created film can be coated with a metal or left as is, depending on the use.
Construction and Working of Film Capacitor
- The generic method of development for these capacitors begins with the removal of a thin layer of plastic film. This film’s thickness determines the capacitance value. Since the capacitance value increases with a decrease in the gap between the electrodes, the higher capacitance value is thus indicated by the lower film thickness. The standard capacitance value for these capacitors, in general, ranges from 1nF to 30muF.
- Once the film is removed according to the desired capacitance value and the breakdown voltage, either aluminum or zinc is metalized and rolled over to form a mother roll.’ The films are only interlaced between sheets of aluminum foil to form the roll in the case of a film/foil capacitor. A flow diagram of the different steps involved in producing a metalized film capacitor is shown in the figure below.
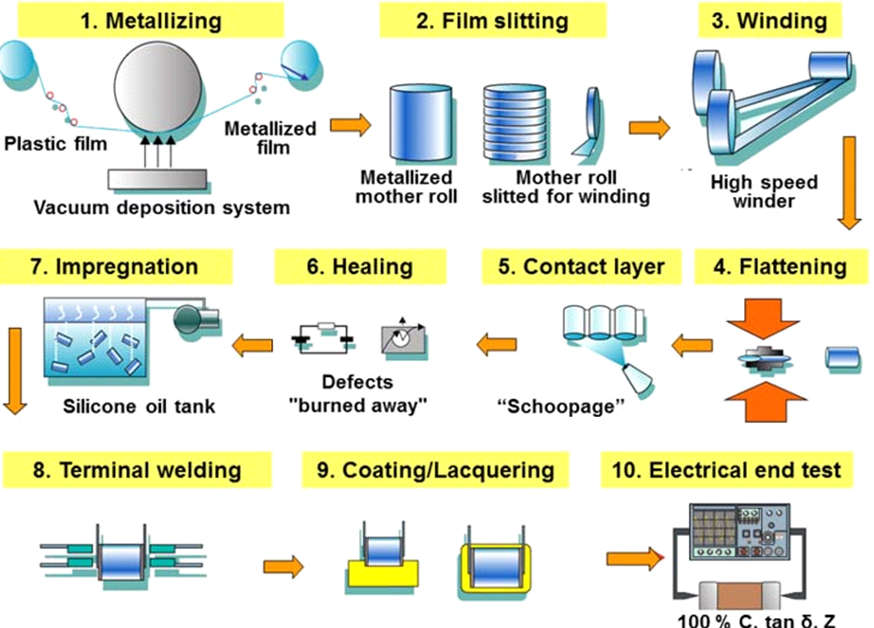
- This roll is then manipulated to accommodate the capacitor size and the desired electrical characteristics by several processes such as slitting, winding, and flattening. The projecting electrodes are subjected to a metalizing process called ‘Schoopage’ until the capacitor obtains its desired shape and size. To create a protective coating on the electrodes, liquefied metals such as zinc, aluminum, or tin are used here. To burn away any existing defects on the electrode surface, the lateral ends of the winding are then sprayed with compressed air and then exposed to a voltage.
- Since the capacitors can be easily influenced by moisture, silicone oil, or some other insulating fluid is impregnated with the winding. Finally, this winding is prepared to be soldered to the capacitor’s metallic terminals. The capacitor is subjected to a final round of protection coating until soldered, where its body is dipped into a protected coating or potted on the outer casing.
Film Capacitor Types
There are several film condensers in which the plastic films are put between the aluminum foils and there are others in which the plastic film is metalized by a phase in which the metal is coated on the film itself. In general, based on construction, film capacitors can be divided narrowly into two groups.
1. Film/Foil Capacitor:
- The film/foil capacitor, as the name implies, uses plastic films as a dielectric and is mounted within two layers of aluminum foil electrodes. These interleaved layers are so organized that they do not touch each other with the metallic layers. Such capacitors can be either non-inductive or inductive.
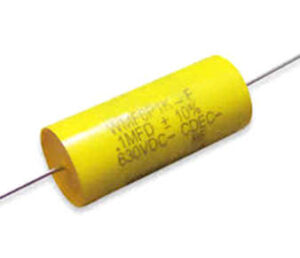
- In such a way that the aluminum foils are located in the middle of the two films, an inductive film foil capacitor is wound. The aluminum foils are not directly attached but through a leading wire that carries the entire winding.
- In such a way that the aluminum foils are located in the middle of the two films, an inductive film foil capacitor is wound. The aluminum foils are not directly attached but through a leading wire that carries the entire winding. A pictorial representation of it is shown in Figure 1.
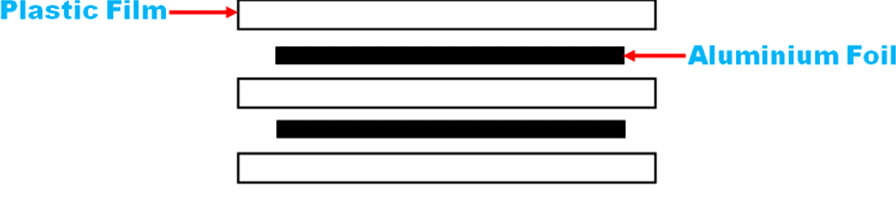
- In a non-inductive fill foil capacitor, the aluminum foils are arranged in such a way that each foil is positioned to a certain degree out of the films, such as that shown in Figure 2.
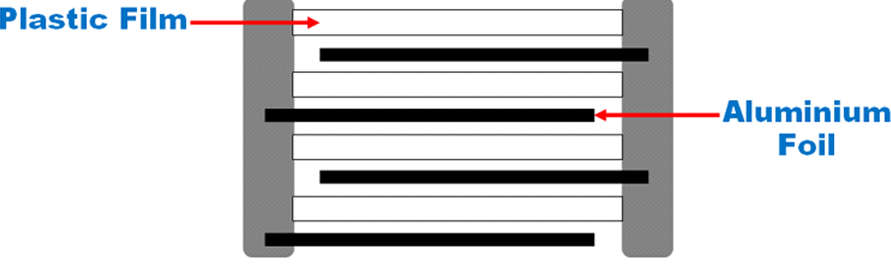
Characteristics of Plastic Film Capacitor
- High insulation resistance.
- Good capacitance stability.
- High efficiency even at high frequency.
- Dielectric used: Polypropelene(PP)/ Polyethylene terephthalate (PET)/Polytetrafluoroethylene(PTFE).
Applications of Plastic Film Capacitor
- The film/foil capacitor application depends on the type of dielectric used. For coupling, decoupling, and bypassing, PET Film/foil capacitors are great. PP Film/Foil (PP) capacitors are a good choice for use in circuits requiring high switching frequencies, such as resonant and oscillator circuits, power supplies, etc.
2. Metalized Film Capacitor:
- The primary distinction between a film foil capacitor and a metalized capacitor is that the metallic electrodes are fused into either side of the dielectric plastic in the latter instead of layering. While it raises the cost and also adds a step to the production process, it has greater reliability and smaller dimensions than a film foil condenser. To get the desired capacitance value, the thickness of the plastic film can be as low as 0.6μm.
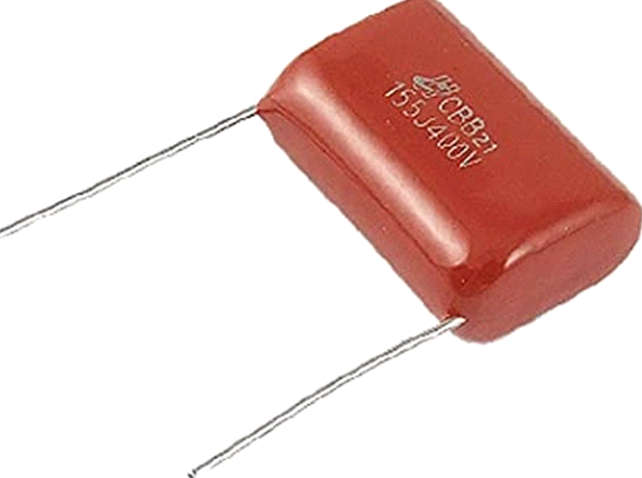
Characteristics of Metalized Film Capacitor
- Self-healing property: This property helps the capacitor repair itself if the electrodes are exposed to each other instead of being short-circuited. This increases the capacitor reliability.
- Compact in dimension and form.
- Polypropylene(PP)/polyethylene terephthalate(PET)/ polytetrafluoroethylene(PTFE)/ polyphenylene sulfide Dielectric used: polypropylene(PP)/polyethylene terephthalate (PET) (PPS).
Applications of Metalized Film Capacitor
- In electronic control circuits, including DC link circuits, pulse circuits, switching circuits, etc., metallic film capacitors are commonly used. In decoupling and filtering applications, the low-power metalized film capacitor finds use.
Uses of Film Capacitor
There are various applications in which these capacitors are used.
- The ‘Power Film Capacitors’ is utilized in the Electronic Devices where power is the major concern in the flashes of ‘X-Rays’, Analog to Digital Converters … these are used.
- To provide the Smoothing effect these capacitors are used.
- It can be preferred as the ‘Energy Storage’ units or components.
- In the operation and the starting of lights made of fluorescent. It used to have ‘Ballasts‘. But in this case, the ‘Power Factor is less. To overcome these Film capacitors are utilized.
- The circuits that are designed for protecting devices make use of Film Capacitors.
- In this way, these capacitors have many popular uses.
- Film capacitors are very simple and easy to analyze and construct. These are known for their stability. It has a very low manufacturing cost. Even at the signals that possess high frequency by the usage of these capacitors, the losses get minimized.